Recent thinking
-
A new chapter: Time to prepare for the next phase of the real estate cycle
17 Jul 2024
David Hedalen and Jonathan Bayfield from our real assets research team highlight data that shows real estate markets in the UK and Europe may be on the brink of an important shift.
-
Boosting low-carbon investment in the UK: A Policy Roadmap
16 Jul 2024
Our in-depth Roadmap for the UK’s journey towards a low-carbon economy contains policy recommendations to unlock private investment in the transition.
-
Liquidity optimisation for insurers: Building a bespoke portfolio solution
9 Jul 2024
In the third part of our liquidity optimisation series, we look at how bespoke liquidity portfolios that take into account the interplay between different assets can suit the needs of insurers.
-
The future of green premia in real estate, part two: Searching for value and resilience
8 Jul 2024
Do energy-efficient buildings have more pricing power, and what could that mean for those investing in the built environment? We bring together the views of leading capital markets researchers, a valuer and an asset manager for the second part of our deep dive into green premia, analysing the investment implications.
-
Finding the right blend: Optimising asset allocation in liquidity pools
5 Jul 2024
In the second part of our new article series on liquidity optimisation, Alastair Sewell investigates how investors can find the right mix of assets for their liquidity pools.
-
The difficult last mile: Inflation, Treasury supply and the outlook for global sovereign bonds
4 Jul 2024
With the focus shifting from interest rate cuts to the likelihood of rates staying higher for longer, Steve Ryder and Daniel Bright assess the possible outcomes and implications of higher rates and monetary policy divergence in debt markets.
-
Avoid, reduce, remove, align: Finding climate transition investment opportunities in real assets
3 Jul 2024
In this article, Luke Layfield and Zoe Austin explain four key pillars that can help real asset investors align their strategies with the climate transition and uncover opportunities to deliver attractive returns.
-
Bond Voyage: A journey into fixed income
2 Jul 2024
In a special European Championships edition of Bond Voyage, we discuss topical themes in liquidity, emerging-market debt, investment-grade credit and global sovereign bonds (with a little help from Cristiano Ronaldo and Kylian Mbappé).
-
A bigger splash: How much liquidity do I need?
1 Jul 2024
The importance of holding liquidity is well understood by large institutions. But how much is enough? In the first part of our new article series on liquidity optimisation, Alastair Sewell investigates the key considerations for different investor types.
-
The future of green premia in real estate, part one: The view from the ground
27 Jun 2024
Do greener buildings have more pricing power, and if so, how much? We bring together the views of leading capital markets researchers, a valuer and an asset manager for a two-part deep dive on the latest market dynamics.
-
Blueprints for a greener economy: Creating a transition planning ecosystem
25 Jun 2024
National transition plans can give investors support, confidence and direction to accelerate the flow of finance to bring about a low-carbon economy. As such, they should be seen as a strategic opportunity.
-
Nothing to fear: Sustainable investing trade-offs
19 Jun 2024
Sustainable investing, and the supposed trade-offs involved, have been a topic of heated debate. But trade-offs are a fundamental part of all types of investment; the key is to be clear about your objectives, as Mirza Baig explains.
-
Bond Voyage: A journey into fixed income
10 Jun 2024
This month, we discuss fiscal discipline in emerging markets, investment-grade credit portfolio construction, potential opportunities for sovereign investors in Canada and the merits of a developed-market focus in global high yield.
-
Multi-asset allocation views: Three faces of reflation
6 Jun 2024
Reflation – another word for increasing economic activity, with an undertone that inflation isn't consistently falling – has been the dominant theme for investors so far in 2024. Sunil Krishnan explores how it is affecting bonds, equities and commodities.
-
Emerging-market debt turns the corner: The EM investment universe grows amid improved resilience
21 May 2024
Emerging-market debt analyst Carmen Altenkirch reports back from the recent International Monetary Fund (IMF)/World Bank meetings in Washington.
-
See the wood, not just the trees: How climate-focused credit investors can help drive real-world change
14 May 2024
Green bond funds and Paris-aligned benchmarks are aimed at climate-focused credit investors who also want the simplicity of passive investing. But while they decarbonise portfolios, they exclude the companies in the real economy that need to transition if the world is to meet the Paris Agreement goals. This is why an active approach can be beneficial.
House View
No one can predict the future. But our quarterly House View sets out the collective wisdom of our investment teams on the current state of global markets – and where they might be heading.
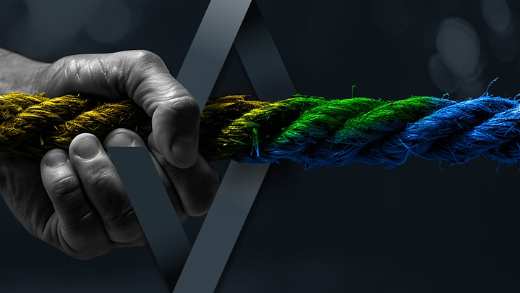
The Little Book of Data
Good data visualisation makes us see the world anew. The sixth edition of The Little Book of Data presents original and curated visuals, charts and graphics to offer a fresh perspective on topics shaping our world.
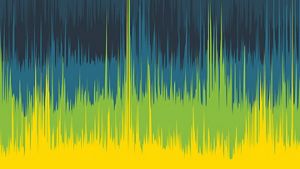
Equities
-
Equity income megatrends: Four themes reshaping the landscape for income investors
In this article, Richard Saldanha takes a look at four megatrends that are likely to transform companies and markets over the coming years, and how they might create opportunities for equity investors.
-
Casting a wider net: Equity income investors find opportunities in global tech and industrials
Large tech firms such as Meta have announced they will pay dividends for the first time in 2024, illustrating the opportunities equity income investors can find beyond “traditional” dividend-paying stocks, argues Richard Saldanha in this Q&A.
-
The ‘In’ crowd: Why companies with ‘club’ dynamics can represent opportunities
Francois de Bruin explores how creating “clubs” can bolster network effects, enhance firms’ resilience and make them attractive to investors.
-
Tech’s tightening grip: What rising US stock concentration means for equity investors
Soaring technology share prices have driven US stock market concentration to unprecedented levels and pushed the US market to a record premium relative to other markets. While both trends could persist, investors need to be aware of the implications, argue Richard Saldanha and Joao Toniato.
-
The war on bugs: Climate change contributes to growth in the pest-control industry
Pest control has become a growing priority for city residents and authorities all year round, as rising temperatures and other factors boost the populations of many pest species. But in creating adaptation solutions, the sector could also represent a long-term investment opportunity.
-
Measure for measure: Why the business of benchmarks matters to investors
Investors rely on benchmarks for data – but benchmarks can also represent investment opportunities in themselves. So how can we identify companies whose benchmarks are likely to have staying power?
-
From cash rich to cash strapped? Why the US consumer boom could run out of road
Our investment teams explain why buoyant US consumer spending will have to weaken eventually. That could pose problems for debt-laden consumer-facing companies.
-
Softly does it? A Q&A with Peter Fitzgerald and Ian Pizer
The managers of the AIMS Target Return strategy explain why the prospects for a range of asset classes suddenly look much brighter.
-
China versus the West:The ongoing rise of economic nationalism
The US and China continue to trade blows as each side looks to limit the other’s access to vital products. With industrial policies also making a comeback, companies are having to navigate a rapidly changing business environment. We look at the key implications for investors.
-
Multi-asset allocation views: Cutting through the noise
Issues around US tech, China, US Treasuries and Japanese monetary policy have hit the headlines in recent weeks. Sunil Krishnan explains how taking a long-term view can help multi-asset investors cut through the noise.
-
Tipping points and transformation: Getting on the right side of change
Rapid changes in the global economy could tip some sectors into low-carbon phases faster than incumbents expect, with important investment implications.
-
Defensive sectors offer value amid AI frenzy: What next for global equity income investors?
Dividends proved resilient in the first half of 2023. Richard Saldanha considers what the rest of the year might have in store for income investors.
-
Supercharge me: The power of network effects
Network effects can boost a company’s growth and build durability – when combined with other strengths, argues Francois de Bruin.
-
What does the data say? Three charts for multi-asset investors
We take a visual approach to explain what’s happening with the US debt ceiling, LVMH and gold.
-
Buy it or build it: Why innovation is key in healthcare
Healthcare is a dynamic industry, but patent expiries from 2025 and drug-price reform in the US pose challenges. Innovation will be key for continued success, as experts from our credit, equity and ESG teams explain.
-
Fragilities exposed as cheap money disappears
Cracks have begun to emerge in the banking sector in recent weeks. As the tide of cheap money that has flooded financial markets for more than a decade ebbs, members of our investment teams are on the lookout for other signs of distress.
Fixed income
-
Liquidity optimisation for insurers: Building a bespoke portfolio solution
In the third part of our liquidity optimisation series, we look at how bespoke liquidity portfolios that take into account the interplay between different assets can suit the needs of insurers.
-
Finding the right blend: Optimising asset allocation in liquidity pools
In the second part of our new article series on liquidity optimisation, Alastair Sewell investigates how investors can find the right mix of assets for their liquidity pools.
-
The difficult last mile: Inflation, Treasury supply and the outlook for global sovereign bonds
With the focus shifting from interest rate cuts to the likelihood of rates staying higher for longer, Steve Ryder and Daniel Bright assess the possible outcomes and implications of higher rates and monetary policy divergence in debt markets.
-
Bond Voyage: A journey into fixed income
In a special European Championships edition of Bond Voyage, we discuss topical themes in liquidity, emerging-market debt, investment-grade credit and global sovereign bonds (with a little help from Cristiano Ronaldo and Kylian Mbappé).
-
Bond Voyage: A journey into fixed income
This month, we discuss fiscal discipline in emerging markets, investment-grade credit portfolio construction, potential opportunities for sovereign investors in Canada and the merits of a developed-market focus in global high yield.
-
Emerging-market debt turns the corner: The EM investment universe grows amid improved resilience
Emerging-market debt analyst Carmen Altenkirch reports back from the recent International Monetary Fund (IMF)/World Bank meetings in Washington.
-
See the wood, not just the trees: How climate-focused credit investors can help drive real-world change
Green bond funds and Paris-aligned benchmarks are aimed at climate-focused credit investors who also want the simplicity of passive investing. But while they decarbonise portfolios, they exclude the companies in the real economy that need to transition if the world is to meet the Paris Agreement goals. This is why an active approach can be beneficial.
-
Bond Voyage: A journey into fixed income
This month, we discuss Spring meetings, the path for rates and sustainability-linked bonds.
-
Bond Voyage: A journey into fixed income
In the April edition of our monthly series, we explore the latest developments in fixed-income markets.
-
Bond Voyage: A journey into fixed income
In the latest instalment of our monthly series, our investment-grade, high-yield, emerging-market and global sovereign bond teams explore the key talking points in fixed income.
-
Too hot, too cold, or just right? The outlook for investment-grade credit
Investment-grade credit has had an encouraging start to 2024 – but are these really “Goldilocks” conditions for the asset class? In their latest Q&A, James Vokins and Chris Higham from our credit team discuss opportunities and risks in this market.
-
Credit spreads and climate solutions: The outlook for climate-focused bond investors
For the first time in three years, interest rates should no longer be a headwind for credit markets in 2024, but other forms of uncertainty may affect climate-aware bond investors. Our credit experts discuss the key themes they expect to play out over the coming months.
-
Bond Voyage: A journey into fixed income
In the latest instalment of our monthly series, our investment-grade, high-yield, emerging-market and global sovereign bond teams look ahead to the key themes that are likely to shape fixed-income markets in 2024.
-
The tide turns: The outlook for fixed income in 2024
After a challenging period for fixed-income markets, conditions look to be right for a better year in bonds.
-
Bond Voyage: A journey into fixed income
In this new year instalment of our monthly series, our investment-grade, high-yield, emerging-market and global sovereign bond teams share their fixed-income resolutions.
-
Rates, regulation and the dash for cash: The outlook for liquidity investors in 2024
Alastair Sewell answers the seven key questions on the minds of liquidity investors heading into 2024.
Real assets
-
A new chapter: Time to prepare for the next phase of the real estate cycle
David Hedalen and Jonathan Bayfield from our real assets research team highlight data that shows real estate markets in the UK and Europe may be on the brink of an important shift.
-
The future of green premia in real estate, part two: Searching for value and resilience
Do energy-efficient buildings have more pricing power, and what could that mean for those investing in the built environment? We bring together the views of leading capital markets researchers, a valuer and an asset manager for the second part of our deep dive into green premia, analysing the investment implications.
-
Avoid, reduce, remove, align: Finding climate transition investment opportunities in real assets
In this article, Luke Layfield and Zoe Austin explain four key pillars that can help real asset investors align their strategies with the climate transition and uncover opportunities to deliver attractive returns.
-
The future of green premia in real estate, part one: The view from the ground
Do greener buildings have more pricing power, and if so, how much? We bring together the views of leading capital markets researchers, a valuer and an asset manager for a two-part deep dive on the latest market dynamics.
-
Cyclical, structural, vintage: The outlook for real estate equity
High inflation and rising rates hit activity in real estate markets over the past year. But cautious optimism is now returning to the investment landscape in the UK and Europe, say Imogen Ebbs and George Fraser-Harding.
-
Building better: Opportunities for DC schemes to invest in the climate transition through real assets
By investing in climate-aligned real assets, defined-contribution pension schemes can help propel the transition while also benefiting from portfolio diversification and attractive risk-adjusted returns, says Mark Meiklejon.
-
Resilience and recovery: The outlook for real estate long income
Renos Booth, Isabel Gossling and Kris McPhail from our real estate long income team consider the outlook for long-lease assets after a challenging period for investors.
-
Rents, rates and the refinancing gap: The outlook for real estate debt
After a challenging 12 months for real estate debt investors, Gregor Bamert discusses what lies ahead for the market in 2024.
-
Illiquidity premia in private debt: Q4 2023
In our latest real assets deep dive, our research team crunches the data to see how evolving macro conditions are reflected in private debt returns.
-
Des res: Opportunities in rental housing for institutional investors
Jonathan Bayfield examines the fundamentals of this asset class, as well as the opportunities and risks for real-estate investors.
-
Common ground: Earning a social licence to operate in real asset investing
Successful real asset investing requires acceptance of asset managers’ practices and procedures from a variety of stakeholders. We explore what this means for managers, their clients and investment outcomes.
-
Plus ça change…The outlook for infrastructure debt in 2024
Infrastructure demonstrated characteristic resilience in 2023 in the face of significant macroeconomic headwinds. Darryl Murphy from our infrastructure team explains why he expects current themes to persist in 2024.
-
Tech, trees and tailwinds: The outlook for climate transition real assets
In this Q&A, James Tarry and Luke Layfield explore the themes shaping the landscape for real asset investors with a climate transition focus.
-
Changing course: Creating a stable investment framework for offshore wind
Better market mechanisms and grid connection arrangements are essential to restore a stable investment environment in the offshore wind sector, as Nick Molho explains.
-
Illiquidity premia in real assets: Q3 2023
Our real assets research team crunch the data to see how evolving macro conditions are reflected in private market returns.
-
Against the current: Seeking resilience in real estate equity
A broad-based recovery in UK and European real estate looks unlikely in 2023, but discerning investors can still find value, say Imogen Ebbs and George Fraser-Harding.
Economic research
-
Boosting low-carbon investment in the UK: A Policy Roadmap
Our in-depth Roadmap for the UK’s journey towards a low-carbon economy contains policy recommendations to unlock private investment in the transition.
-
Blueprints for a greener economy: Creating a transition planning ecosystem
National transition plans can give investors support, confidence and direction to accelerate the flow of finance to bring about a low-carbon economy. As such, they should be seen as a strategic opportunity.
-
Nothing to fear: Sustainable investing trade-offs
Sustainable investing, and the supposed trade-offs involved, have been a topic of heated debate. But trade-offs are a fundamental part of all types of investment; the key is to be clear about your objectives, as Mirza Baig explains.
-
The tipping point for climate finance: Making financial flows consistent with the Paris Agreement
Transition plans, including from governments in response to the Global Stocktake, will be crucial to bring about the shift to a low-emissions, climate-resilient world. Markets need clear implementation signals to align capital with the goals of the Paris Agreement. Our in-depth report calls for the creation of a transition-plan ecosystem connecting all levels of the global economy.
-
China versus the West:The ongoing rise of economic nationalism
The US and China continue to trade blows as each side looks to limit the other’s access to vital products. With industrial policies also making a comeback, companies are having to navigate a rapidly changing business environment. We look at the key implications for investors.
-
Disability inclusion in the workplace: Taking down the barriers
Disabled employees continue to face a variety of hurdles to cope with in addition to their day job. We look at how employers can help remove those barriers to allow everyone to thrive.
-
Accelerating climate solutions: The Edinburgh Earth Initiative in profile
In the 17th and 18th centuries, academics at the University of Edinburgh helped drive the Industrial Revolution. Today, they are connecting with businesses to tackle the climate emergency. Words by Miles Costello.
-
Buy it or build it: Why innovation is key in healthcare
Healthcare is a dynamic industry, but patent expiries from 2025 and drug-price reform in the US pose challenges. Innovation will be key for continued success, as experts from our credit, equity and ESG teams explain.
-
Getting a taste for fiscal intervention, but at what cost?
Fiscal intervention is, again, a vital part of the government policy toolkit, supporting plans to boost domestic industries and fight climate change. But while well-intended, such measures will add to already elevated debt levels, with significant implications for investors, as Michael Grady explains.
-
Forget what you think you know: Staying humble in a world of rising risk
In a world where potential pitfalls loom around every corner, Peter Fitzgerald and Ian Pizer explain why investors need to look beyond what financial models are telling them to keep portfolios resilient to the challenges ahead.
-
Fragilities exposed as cheap money disappears
Cracks have begun to emerge in the banking sector in recent weeks. As the tide of cheap money that has flooded financial markets for more than a decade ebbs, members of our investment teams are on the lookout for other signs of distress.
-
What does the data say? Five charts on financial fragilities
We take a visual approach to explain what’s happening with banks.
-
LGBTQ+ inclusion in the workplace: Creating psychological safety
Each experience is unique, but lesbian, gay, bisexual, transgender, non-binary and other non-heteronormative people (LGBTQ+) still face huge challenges, in and out of the workplace. Companies should do more to support them and foster a culture of inclusion.
-
Boom! Shake the gloom? Does China’s reopening mark a new beginning?
China looks set for a rapid economic rebound in the first quarter after finally abandoning its zero-COVID policy. But will the recovery prove temporary as longer-term dynamics reassert themselves?
-
Engaging on neurodiversity: What can be learned from other DE&I initiatives
Many diversity, equity and inclusion initiatives have seen improvements in recent years, but neurodiversity has not progressed at the same pace. Abigail Herron explores what can be applied from other successful DE&I campaigns to put neurodiversity firmly in the spotlight.
-
Why inflation is likely to prove sticky
Central banks will find it far harder to eradicate inflation than markets anticipate and will be in no hurry to ease off on rate hikes, argues Ian Pizer.
Insurance
-
Boosting low-carbon investment in the UK: A Policy Roadmap
Our in-depth Roadmap for the UK’s journey towards a low-carbon economy contains policy recommendations to unlock private investment in the transition.
-
Blueprints for a greener economy: Creating a transition planning ecosystem
National transition plans can give investors support, confidence and direction to accelerate the flow of finance to bring about a low-carbon economy. As such, they should be seen as a strategic opportunity.
-
Nothing to fear: Sustainable investing trade-offs
Sustainable investing, and the supposed trade-offs involved, have been a topic of heated debate. But trade-offs are a fundamental part of all types of investment; the key is to be clear about your objectives, as Mirza Baig explains.
-
The tipping point for climate finance: Making financial flows consistent with the Paris Agreement
Transition plans, including from governments in response to the Global Stocktake, will be crucial to bring about the shift to a low-emissions, climate-resilient world. Markets need clear implementation signals to align capital with the goals of the Paris Agreement. Our in-depth report calls for the creation of a transition-plan ecosystem connecting all levels of the global economy.
-
China versus the West:The ongoing rise of economic nationalism
The US and China continue to trade blows as each side looks to limit the other’s access to vital products. With industrial policies also making a comeback, companies are having to navigate a rapidly changing business environment. We look at the key implications for investors.
-
Disability inclusion in the workplace: Taking down the barriers
Disabled employees continue to face a variety of hurdles to cope with in addition to their day job. We look at how employers can help remove those barriers to allow everyone to thrive.
-
Accelerating climate solutions: The Edinburgh Earth Initiative in profile
In the 17th and 18th centuries, academics at the University of Edinburgh helped drive the Industrial Revolution. Today, they are connecting with businesses to tackle the climate emergency. Words by Miles Costello.
-
Buy it or build it: Why innovation is key in healthcare
Healthcare is a dynamic industry, but patent expiries from 2025 and drug-price reform in the US pose challenges. Innovation will be key for continued success, as experts from our credit, equity and ESG teams explain.
-
Getting a taste for fiscal intervention, but at what cost?
Fiscal intervention is, again, a vital part of the government policy toolkit, supporting plans to boost domestic industries and fight climate change. But while well-intended, such measures will add to already elevated debt levels, with significant implications for investors, as Michael Grady explains.
-
Forget what you think you know: Staying humble in a world of rising risk
In a world where potential pitfalls loom around every corner, Peter Fitzgerald and Ian Pizer explain why investors need to look beyond what financial models are telling them to keep portfolios resilient to the challenges ahead.
-
Fragilities exposed as cheap money disappears
Cracks have begun to emerge in the banking sector in recent weeks. As the tide of cheap money that has flooded financial markets for more than a decade ebbs, members of our investment teams are on the lookout for other signs of distress.
-
What does the data say? Five charts on financial fragilities
We take a visual approach to explain what’s happening with banks.
-
LGBTQ+ inclusion in the workplace: Creating psychological safety
Each experience is unique, but lesbian, gay, bisexual, transgender, non-binary and other non-heteronormative people (LGBTQ+) still face huge challenges, in and out of the workplace. Companies should do more to support them and foster a culture of inclusion.
-
Boom! Shake the gloom? Does China’s reopening mark a new beginning?
China looks set for a rapid economic rebound in the first quarter after finally abandoning its zero-COVID policy. But will the recovery prove temporary as longer-term dynamics reassert themselves?
-
Engaging on neurodiversity: What can be learned from other DE&I initiatives
Many diversity, equity and inclusion initiatives have seen improvements in recent years, but neurodiversity has not progressed at the same pace. Abigail Herron explores what can be applied from other successful DE&I campaigns to put neurodiversity firmly in the spotlight.
-
Why inflation is likely to prove sticky
Central banks will find it far harder to eradicate inflation than markets anticipate and will be in no hurry to ease off on rate hikes, argues Ian Pizer.
Pensions
-
Boosting low-carbon investment in the UK: A Policy Roadmap
Our in-depth Roadmap for the UK’s journey towards a low-carbon economy contains policy recommendations to unlock private investment in the transition.
-
Blueprints for a greener economy: Creating a transition planning ecosystem
National transition plans can give investors support, confidence and direction to accelerate the flow of finance to bring about a low-carbon economy. As such, they should be seen as a strategic opportunity.
-
Nothing to fear: Sustainable investing trade-offs
Sustainable investing, and the supposed trade-offs involved, have been a topic of heated debate. But trade-offs are a fundamental part of all types of investment; the key is to be clear about your objectives, as Mirza Baig explains.
-
The tipping point for climate finance: Making financial flows consistent with the Paris Agreement
Transition plans, including from governments in response to the Global Stocktake, will be crucial to bring about the shift to a low-emissions, climate-resilient world. Markets need clear implementation signals to align capital with the goals of the Paris Agreement. Our in-depth report calls for the creation of a transition-plan ecosystem connecting all levels of the global economy.
-
China versus the West:The ongoing rise of economic nationalism
The US and China continue to trade blows as each side looks to limit the other’s access to vital products. With industrial policies also making a comeback, companies are having to navigate a rapidly changing business environment. We look at the key implications for investors.
-
Disability inclusion in the workplace: Taking down the barriers
Disabled employees continue to face a variety of hurdles to cope with in addition to their day job. We look at how employers can help remove those barriers to allow everyone to thrive.
-
Accelerating climate solutions: The Edinburgh Earth Initiative in profile
In the 17th and 18th centuries, academics at the University of Edinburgh helped drive the Industrial Revolution. Today, they are connecting with businesses to tackle the climate emergency. Words by Miles Costello.
-
Buy it or build it: Why innovation is key in healthcare
Healthcare is a dynamic industry, but patent expiries from 2025 and drug-price reform in the US pose challenges. Innovation will be key for continued success, as experts from our credit, equity and ESG teams explain.
-
Getting a taste for fiscal intervention, but at what cost?
Fiscal intervention is, again, a vital part of the government policy toolkit, supporting plans to boost domestic industries and fight climate change. But while well-intended, such measures will add to already elevated debt levels, with significant implications for investors, as Michael Grady explains.
-
Forget what you think you know: Staying humble in a world of rising risk
In a world where potential pitfalls loom around every corner, Peter Fitzgerald and Ian Pizer explain why investors need to look beyond what financial models are telling them to keep portfolios resilient to the challenges ahead.
-
Fragilities exposed as cheap money disappears
Cracks have begun to emerge in the banking sector in recent weeks. As the tide of cheap money that has flooded financial markets for more than a decade ebbs, members of our investment teams are on the lookout for other signs of distress.
-
What does the data say? Five charts on financial fragilities
We take a visual approach to explain what’s happening with banks.
-
LGBTQ+ inclusion in the workplace: Creating psychological safety
Each experience is unique, but lesbian, gay, bisexual, transgender, non-binary and other non-heteronormative people (LGBTQ+) still face huge challenges, in and out of the workplace. Companies should do more to support them and foster a culture of inclusion.
-
Boom! Shake the gloom? Does China’s reopening mark a new beginning?
China looks set for a rapid economic rebound in the first quarter after finally abandoning its zero-COVID policy. But will the recovery prove temporary as longer-term dynamics reassert themselves?
-
Engaging on neurodiversity: What can be learned from other DE&I initiatives
Many diversity, equity and inclusion initiatives have seen improvements in recent years, but neurodiversity has not progressed at the same pace. Abigail Herron explores what can be applied from other successful DE&I campaigns to put neurodiversity firmly in the spotlight.
-
Why inflation is likely to prove sticky
Central banks will find it far harder to eradicate inflation than markets anticipate and will be in no hurry to ease off on rate hikes, argues Ian Pizer.
Responsible investment
-
Boosting low-carbon investment in the UK: A Policy Roadmap
Our in-depth Roadmap for the UK’s journey towards a low-carbon economy contains policy recommendations to unlock private investment in the transition.
-
The future of green premia in real estate, part two: Searching for value and resilience
Do energy-efficient buildings have more pricing power, and what could that mean for those investing in the built environment? We bring together the views of leading capital markets researchers, a valuer and an asset manager for the second part of our deep dive into green premia, analysing the investment implications.
-
Avoid, reduce, remove, align: Finding climate transition investment opportunities in real assets
In this article, Luke Layfield and Zoe Austin explain four key pillars that can help real asset investors align their strategies with the climate transition and uncover opportunities to deliver attractive returns.
-
The future of green premia in real estate, part one: The view from the ground
Do greener buildings have more pricing power, and if so, how much? We bring together the views of leading capital markets researchers, a valuer and an asset manager for a two-part deep dive on the latest market dynamics.
-
Blueprints for a greener economy: Creating a transition planning ecosystem
National transition plans can give investors support, confidence and direction to accelerate the flow of finance to bring about a low-carbon economy. As such, they should be seen as a strategic opportunity.
-
Nothing to fear: Sustainable investing trade-offs
Sustainable investing, and the supposed trade-offs involved, have been a topic of heated debate. But trade-offs are a fundamental part of all types of investment; the key is to be clear about your objectives, as Mirza Baig explains.
-
See the wood, not just the trees: How climate-focused credit investors can help drive real-world change
Green bond funds and Paris-aligned benchmarks are aimed at climate-focused credit investors who also want the simplicity of passive investing. But while they decarbonise portfolios, they exclude the companies in the real economy that need to transition if the world is to meet the Paris Agreement goals. This is why an active approach can be beneficial.
-
Building better: Opportunities for DC schemes to invest in the climate transition through real assets
By investing in climate-aligned real assets, defined-contribution pension schemes can help propel the transition while also benefiting from portfolio diversification and attractive risk-adjusted returns, says Mark Meiklejon.
-
The war on bugs: Climate change contributes to growth in the pest-control industry
Pest control has become a growing priority for city residents and authorities all year round, as rising temperatures and other factors boost the populations of many pest species. But in creating adaptation solutions, the sector could also represent a long-term investment opportunity.
-
Credit spreads and climate solutions: The outlook for climate-focused bond investors
For the first time in three years, interest rates should no longer be a headwind for credit markets in 2024, but other forms of uncertainty may affect climate-aware bond investors. Our credit experts discuss the key themes they expect to play out over the coming months.
-
Common ground: Earning a social licence to operate in real asset investing
Successful real asset investing requires acceptance of asset managers’ practices and procedures from a variety of stakeholders. We explore what this means for managers, their clients and investment outcomes.
-
Plus ça change…The outlook for infrastructure debt in 2024
Infrastructure demonstrated characteristic resilience in 2023 in the face of significant macroeconomic headwinds. Darryl Murphy from our infrastructure team explains why he expects current themes to persist in 2024.
-
Tech, trees and tailwinds: The outlook for climate transition real assets
In this Q&A, James Tarry and Luke Layfield explore the themes shaping the landscape for real asset investors with a climate transition focus.
-
Changing course: Creating a stable investment framework for offshore wind
Better market mechanisms and grid connection arrangements are essential to restore a stable investment environment in the offshore wind sector, as Nick Molho explains.
-
The tipping point for climate finance: Making financial flows consistent with the Paris Agreement
Transition plans, including from governments in response to the Global Stocktake, will be crucial to bring about the shift to a low-emissions, climate-resilient world. Markets need clear implementation signals to align capital with the goals of the Paris Agreement. Our in-depth report calls for the creation of a transition-plan ecosystem connecting all levels of the global economy.
-
The time to lead: Reforming multilateral development banks through a climate lens
To have a chance of limiting global warming to less than two degrees, the world must unlock huge investments in emerging markets. This is prompting calls for the reform of multilateral development banks, but will this be enough?
Subscribe to AIQ
Receive our insights on the big themes influencing financial markets and the global economy, from interest rates and inflation to technology and environmental change.
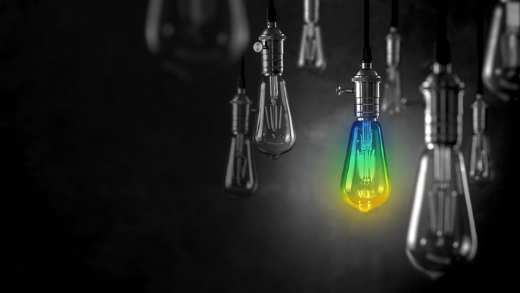